The Effect Of The Affordable Care Act Excise Tax On Medical Devices Packaging.
- Stephen Tansey
- Jun 23, 2014
- 2 min read
There are many arguments in favor of and opposed to the repeal of the 2.3% excise tax on medical devices passed as part of the Affordable Care Act. However, since the tax is projected to generate approximately $20 billion over 10 years, repeal is unlikely. This means that medical device manufacturers will need to find ways to adapt to the new tax.
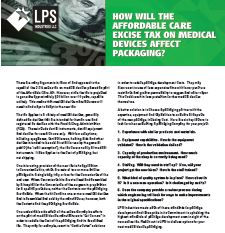
The tax applies to a variety of medical devices, generally defined as devices that are intended for human use and registered as devices with the Food & Drug Administration (FDA). These include dental instruments, dental equipment and devices for research use only. With few exceptions, including eyeglasses, contact lenses, hearing aids and other devices intended to be sold at retail for use by the general public (the “retail exemption”), the tax applies to the value of nearly all medical instruments and devices.
One apparent inconsistent provision of the new tax is its application to packaging for convenience kits, which are sets of two or more instruments or devices packaged in a single bag, tray, or box for the convenience of the end user. When a commercial kit containing medical devices and/or instruments is assembled and sold by the manufacturer the value of the kit is taxable. However, when the same contents are kitted in a hospital for the convenience of the surgeon, the contents but not the packaging were subject to the excise tax when the hospital acquired them.
One undesirable side effect of the excise tax may be efforts on the part of medical device manufactures to “cut corners” in order to reduce the cost of the packaging and its associated tax. They may, for example, resort to “cookie cutter” solutions in order to reduce package development costs. They may also resort to use of less expensive films with lower puncture resistance and greater permeability to oxygen and water vapor. This could result in less protection for the medical devices themselves.
Within the current regulatory environment it is even more important for medical device manufacturers to choose a packaging partner with the expertise, equipment and capabilities to evaluate all aspects of packaging. Here are six factors to look for when evaluating a packaging manufacturer for your project:
Experience with similar products and materials, including foil
Equipment capabilities – How is the equipment validated? How is the validation defined?
Capacity of production environment – How much capacity is currently being used?
Staffing – Will they need to staff up? If so, will your project get the new hires?
What kind of quality system is in place? How robust is it? Any external quality certifications? Is it challenged by audits?
Can the manufacturer supply realistic minimums?
LPS Industries takes pride in its commitment to upholding the highest standards of package development and manufacturing. Contact LPS for more information about medical device packaging.
Kommentare